С помощью 3D-печати наплавлением можно изготовить сложные объемные конструкции. Таким способом сейчас производятся высокоточные антенны сложной формы. По антенне должен течь электрический ток, а значит, требуется использование особых 3D-принтеров, печатающих металлом, что чрезвычайно дорого и сложно в обслуживании. Ближайший аналог — фотополимерные и FDM-принтеры, печатающие пластиком. Хотя структуры, производимые ими, не проводят электрический ток, стоимость такого производства ниже на несколько порядков. Взяв за основу лучшие качества этих технологий, ученые МФТИ разработали новую технологию, основанную на недорогой и простой печати пластиком и последующем электрохимическом покрытии формы металлом. Работа опубликована в журнале Scientific Reports и получила патент на изобретение.
Сегодня качественная и однородная связь в производственных помещениях является жизненно важным условием бесперебойной работы оборудования. Чтобы избежать создания мертвых зон, необходимо устанавливать несколько роутеров Wi-Fi либо создавать специализированные антенны под конкретную задачу, производство которых осложняется их нетривиальной формой.
В лаборатории радиофотоники МФТИ решили рассмотреть недорогие пластмассовые модели, совместимые с различными сплавами. Оказалось, что металлы с высокой проводимостью позволяют достичь превосходных электромагнитных характеристик — обычно для диапазона частот 1–10 ГГц достаточно нескольких микрон меди. Таким образом, с помощью тончайшего металлического слоя на пластмассовой конструкции физики получили высокоточную антенну, стабильно работающую в нужном диапазоне, себестоимость которой намного дешевле стандартной 3D-печати на металле.
Однако проведенные эксперименты показали, что на частотах выше 5 ГГц негативное влияние пластика на излучательную характеристику антенн существенно повышается. Тогда решено было после покрытия формы металлом удалять пластиковую подложку. И оказалось, что металлические антенны без подложки, изготовленные с помощью напыления на форму, работают лучше стандартных антенн, которые также страдают от потерь на высоких частотах. Таким образом, новый экономичный способ создания антенн сможет обеспечить качественной связью 5G и 6G.
«При создании высокоточной антенны первичным фактором являются массово-габаритные характеристики помещения. Именно они закладываются в алгоритм численного моделирования, с помощью которого рассчитывается конфигурация устройства. Обычно это довольно причудливая форма, которую трудно создать руками, но вполне возможно с помощью 3D-принтера», — рассказывает Дмитрий Филонов, руководитель лаборатории радиофотоники Центра фотоники и двумерных материалов МФТИ.
В результате бюджетный метод изготовления сложных антенн с помощью FDM-печати состоит из пяти этапов. Это печать заготовки с помощью проводящего полимера, обработка поверхности для улучшения гладкости, размещение вспомогательных электродов на заготовке, гальваническое покрытие и удаление заготовки. Температура плавления типичных полимеров, используемых в FDM-печати, составляет около 180–230ºC, и электрохимически осажденный металл выдерживает эти температуры.
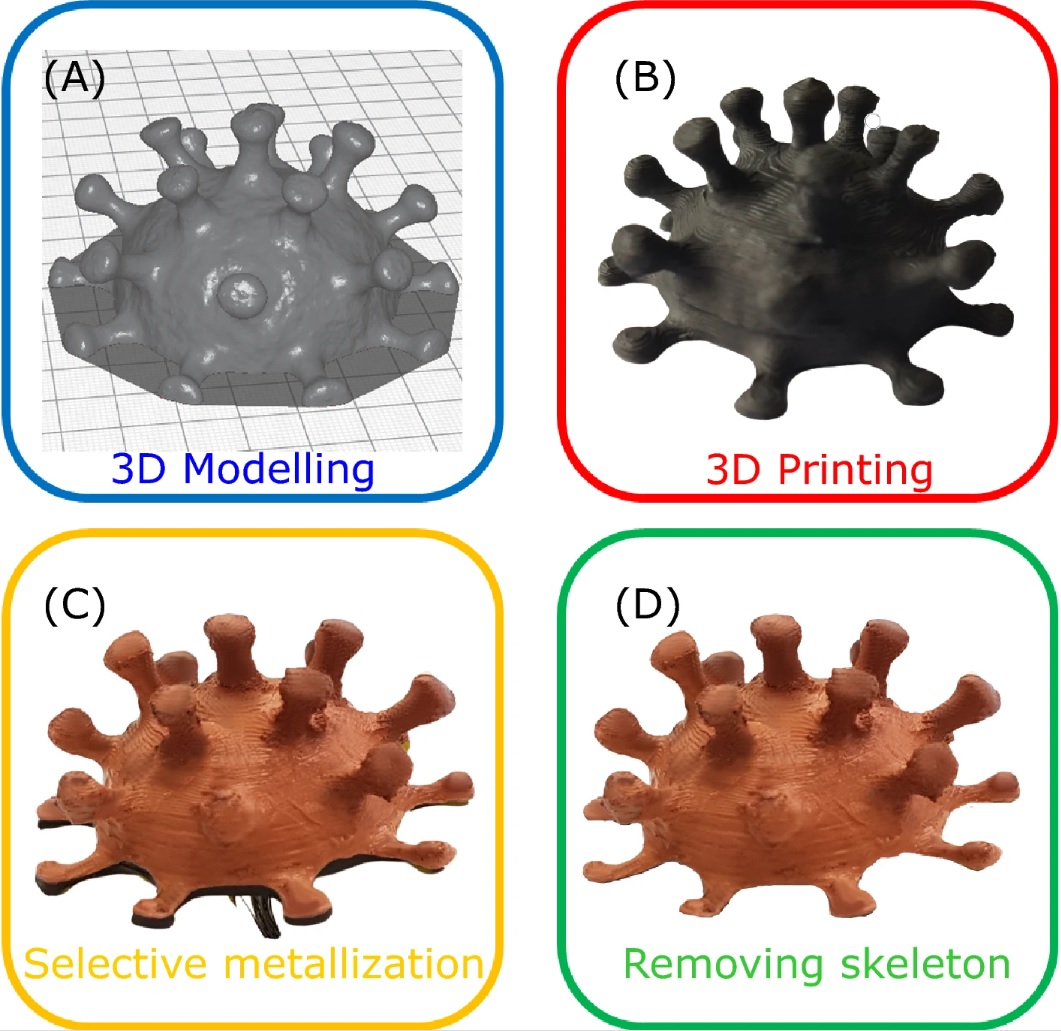
Последовательность самостоятельного прототипирования модели металлического коронавируса. (A) 3D-моделирование. (B) FDM 3D-печать пластикового каркаса. (C) Гальваническое покрытие поверхности прототипа. (D) Удаление пластикового каркаса. Источник: Scientific Reports.
«Хотя наш новый метод не может полноценно конкурировать по производительности с прямой металлической печатью, он способен обеспечить производство надежных конструкций при чрезвычайно низкой стоимости», — подытожил Дмитрий Филонов.
Дальнейшее развитие этой технологии позволит создавать более сложные формы и раскрыть их преимущества в электромагнитных приложениях. Кроме того, предпринимается немало усилий по 3D-печати электронных схем (как пассивных, так и активных элементов). Это сделает возможным послойное наращивание антенны вместе с настраиваемой электроникой. Общая стоимость производства в этом случае значительно снизится.