Выведение полезной нагрузки на земную орбиту, а в обозримом будущем — доставка людей и грузов на расстояния в тысячи и миллионы километров — тема не государственная, а частно-государственная. На наших глазах создание космических ракет перестает быть делом крупных предприятий с историей в десятилетия. Во многих странах возникают стартапы, занимающиеся разработкой собственной ракеты. В России к этому ближе всех подошел центр разработок компании S7, который, в отличие от многих других космических стартапов, начал с освоения новых технологий, до сих пор не используемых в отечественном ракетостроении.
Новосибирск — Кассиопея
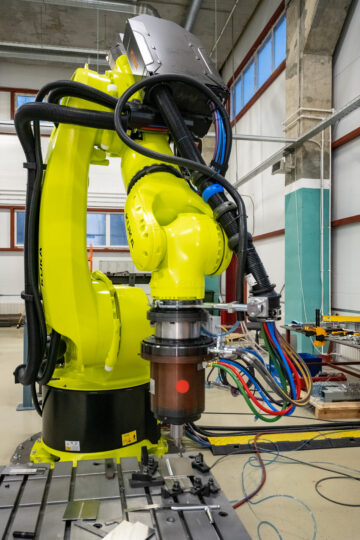
Роботизированный комплекс для сварки трением с перемешиванием
В 2001 году некогда государственная авиакомпания «Сибирь», базирующаяся в новосибирском аэропорту Толмачево, получила от Международной ассоциации воздушного транспорта индивидуальный идентификатор S7. Спустя четыре года была создана группа компаний S7 Group. Первая в мире авиакомпания, поместившая на фюзеляж самолетов свой идентификационный код, успешно развивалась, обзаведясь хабами в Домодедово и Пулково, полностью обновила свой воздушный флот в 2008 году, а спустя десятилетие стала второй по числу перевезенных пассажиров авиакомпанией России. В 2016 году создана компания S7 Space, и в том же году S7 Group купила у РКК «Энергия» космодром «Морской старт».
В начале 2017 года S7 Space получила лицензию на осуществление космической деятельности в России, став первой российской коммерческой компанией, имеющей право предоставлять международные космические услуги. В 2018 году S7 Group была переименована в S7 AirSpace Corporation. Запущены образовательные программы S7. В 2019-м создано подразделение S7 R&D. В 2020 году в МФТИ компания создала кафедру «Информационные технологии в авиации».
Ускорять НТП
С каждым годом становится все более востребованным сектор легких ракет. Просто потому, что все виды спутников — телекоммуникационные, навигационные, предназначенные для зондирования Земли — уменьшаются в размерах и становятся легче. Ракета грузоподъемностью 0,6–2 тонны может поднять множество небольших спутников. Каждый из них теперь способен решать все те задачи, для которых раньше требовались тяжеловесы в несколько тонн. К тому же этих спутников становится все больше: некоторые компании запускают на орбиту группировки из сотен и даже тысяч аппаратов.
Кроме того, космические амбиции появляются у все большего количества государств. Например, некоторые европейские страны, помимо Европейской космической программы, развивают собственные космические проекты: массово производят спутники и создают ракеты-носители. Ведь опыт уже показал, что в рамках частного космического бизнеса это вполне реально, к тому же дешевле и быстрее.
Еженедельно запуская свои ракеты, Илон Маск показал, что без взрывов на старте, взрывов в первые минуты после старта и прочих оказий нет и развития ракетостроения.
SpaceX делает очень дешевые двигатели, которые обеспечивают приемлемую себестоимость запуска ракеты-носителя. При этом двигатель весьма надежен, поскольку в него закладываются весьма средние характеристики с большим конструктивным запасом. Удешевляя коммерческие запуски, компания стала конкурировать по их числу с запусками с Байконура, в конце концов выбившись в лидеры. В 2020 году она доставила на своей новой ракете американских астронавтов к МКС, доказав, что «The trampoline is working» (англ. «Трамплин работает»). Однако этому успеху предшествовали годы разработок и освоения передовых технологий.
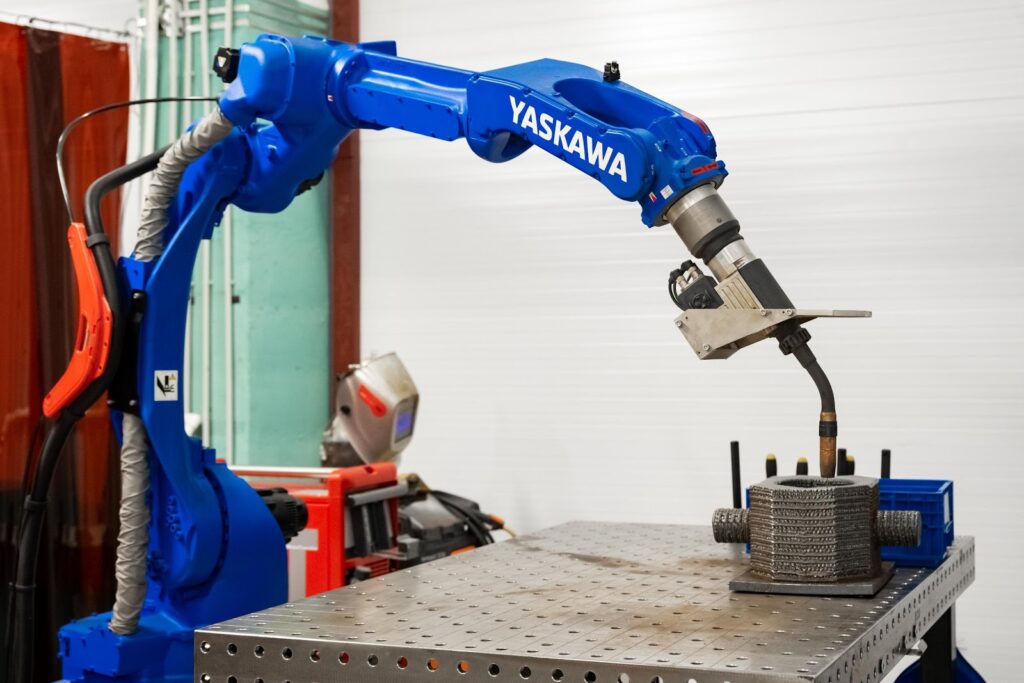
Промышленный робот для дугового выращивания Yaskawa
Две большие разницы
Сергей Сытин, генеральный директор Центра разработок S7:
Мы начали с технологий. Двух лет еще не прошло с начала нашей активной работы. Мы научились пользоваться сваркой трением с перемешиванием (СТП) для обечаек (тонких цилиндрических замкнутых поверхностей). Без этого невозможно создать стрингерно-шпангоутное подкрепление (стрингер — продольный набор усилений конструкции, шпангоут — поперечный, прим. ред.). Никто в России так не использует эту технологию. Мы научились аддитивно выращивать крупногабаритные детали. Они «выпекаются» с помощью программ, которые заложены в роботизированные установки. Тяжелая деталь выращивается несколько суток, но процесс отработан. Весь этот путь мы прошли за полтора года.
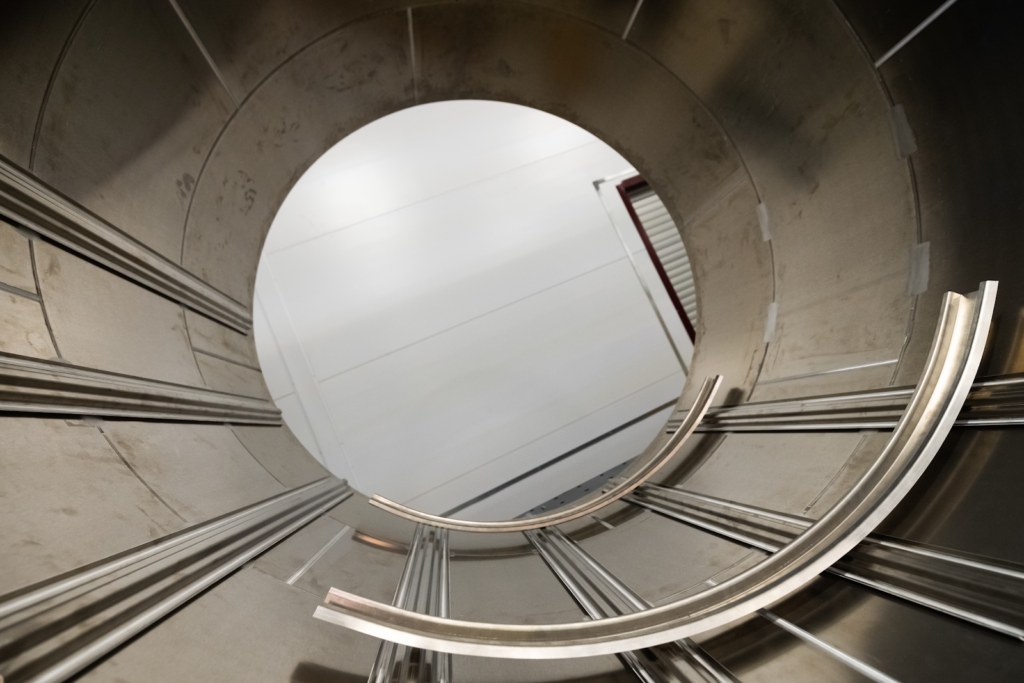
Прототип разработанного стрингерно-шпангоутного подкрепления обечайки ракеты
Ракета — это обычно просто набор баков. Причем чаще всего баки являются и оболочкой ракеты. Аддитивные технологии позволяют производить днища этих баков. Топливный бак — это цилиндрическая обечайка из металлического листа. Для легкой ракеты бак окислителя — гладкий цилиндр, сваренный при помощи СТП с днищами без утолщения в зоне сварки, чего невозможно добиться аргонно-дуговой сваркой. Для этих баков в S7 R&D используют современный алюминиевый сплав отечественной разработки AlMgSc.
Часть модельной конструкции топливного бака ракеты
«Мы все делаем с помощью системы цифрового системного проектирования. Одна из установок, которую мы сами проектируем и сами рассчитываем, будет последовательно изготавливать корпус ракеты. Одно кольцо поставила, потом другое, проварила, подвинула, следующее вставила, пока бак не наберется, потом днище замыкающее проварила — и бак готов. Вот наша разработка, наше моделирование, наше конструирование. Что же касается усиления конструкции, то сравнение классической “вафельной” обечайки и стрингерно-шпангоутной показывает, что последняя опережает по качеству и очень сильно выигрывает технологически. Ее дешевле и проще сделать во всех смыслах, если уметь делать то, чему мы научились», — говорит инженер-конструктор, выпускник Физтеха Илья Якимов.
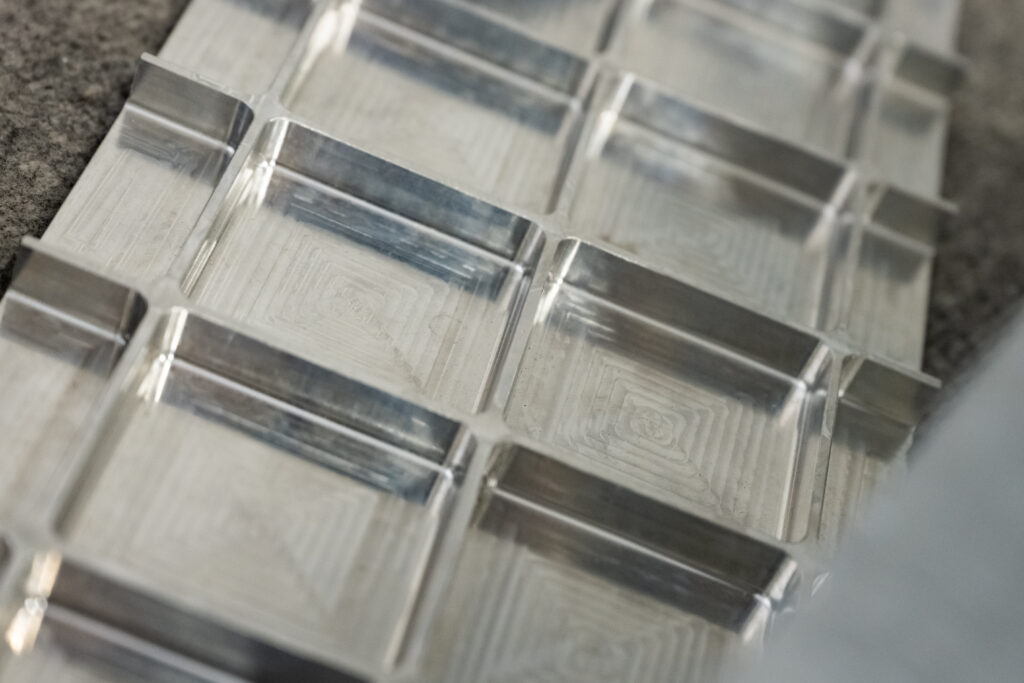
Классическое «вафельное» усиление обечайки
Ах, эта сварка…
От технологий сварки в ракете зависит практически все — и масса, и прочность, и простота производства. При плавлении материала его прочностные свойства в зоне нагрева падают. Поскольку ракета всегда разрушается в самом слабом месте, необходимо сделать ее одинаково прочной всюду. Для этого обычно создают утолщение в зоне сварки. Большее количество плохого материала несет ту же нагрузку, что и меньшее количество материала хорошего. Такова логика традиционной аргонно-дуговой сварки.
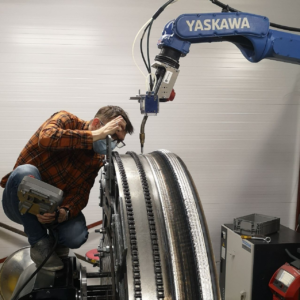
Инженер-технолог Арсений Кисарев контролирует процесс 3D-печати конструкции днища топливного бака
«Мы нашли способ соединить два листа материала без плохой зоны: все наше соединение — одинаково хороший материал. Значит, мы можем не делать утолщения и пользоваться тонкими листами при сборке корпуса: за счет этих зон утолщения набегают тонны лишней массы. К тому же при работе по старинке необходимы очень дорогие станки, выходит дикое количество стружки. А все, что нужно нам, — “поколдовать” над технологией этого соединения. Причем западная ракетная индустрия уже несколько десятилетий использует СТП. Мы берем лист, сгибаем его на вальцах. Потом согнутые листы свариваем. Получается кольцо, такие кольца свариваем между собой. Жидкотопливная ракета — это просто некая композиция баков. Бак горючего, бак окислителя, в нашем случае это пары керосина и кислорода. Стенка бака является несущей стенкой. И нагрузки в десятки тонн эта оболочка держит», — поясняет инженер-технолог Арсений Кисарев.
Для алюминия необходимая нагрузка на этот инструмент составляет порядка одной или нескольких тонн в зависимости от толщины свариваемых листов. Он начинает движение вдоль стыка гладких сплавляемых плоскостей и разогревает алюминий примерно до 400–450℃. Этот металл плавится при 650℃. Поэтому возникает вязкопластическое состояние материала. За счет особых насечек на инструменте он перемешивает этот материал в пластичном состоянии с последующей полной рекристаллизацией.